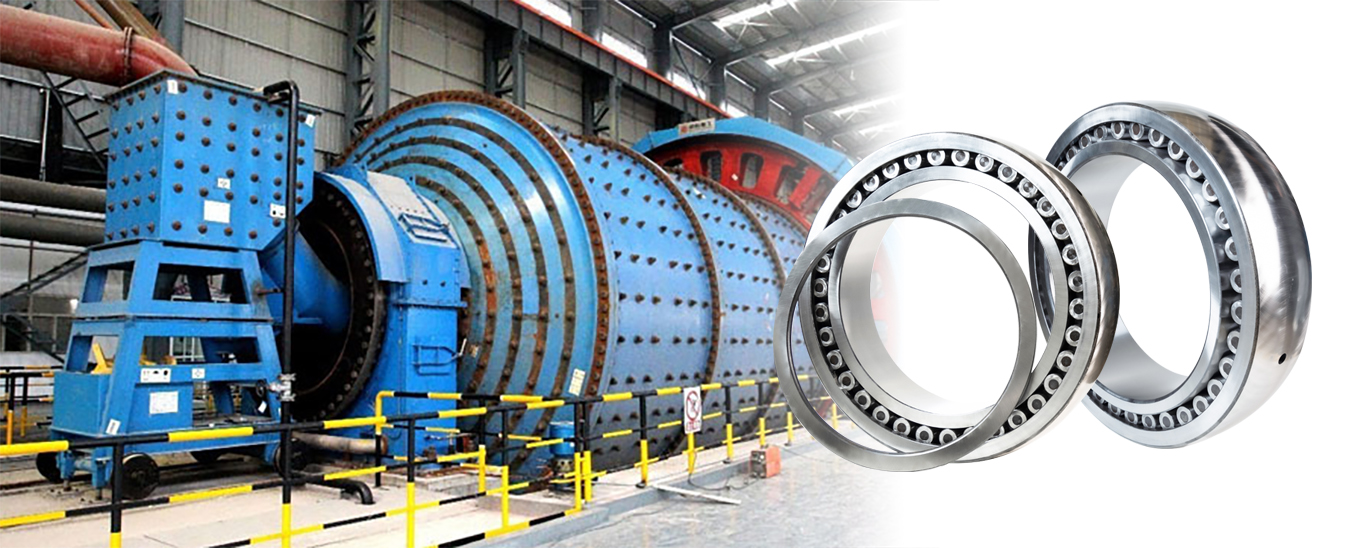
Selection of Traditional Ball Mill Bearings
Traditional spherical roller bearings have the following advantages: firstly, they have high load capacity and impact resistance, can withstand large radial and axial loads, and can adapt to impact and vibration under working conditions. Secondly, it has high rotational accuracy and stability, which can maintain stable rotational performance and motion balance, reduce noise and vibration. Thirdly, it has a long service life and reliability. Due to its reasonable internal structure and good coordination of various components, it can withstand wear and load under working conditions well, extending its service life. Fourthly, it has high adaptability and substitutability, which can adapt to different working environments and application requirements, and can replace other types of bearings, improving the performance and reliability of the equipment. In summary, traditional self-aligning roller bearings have superior characteristics in various aspects and are an important bearing widely used in various mechanical equipment and industrial fields.
Spherical Double Row Roller Bearings
Introduction: The outer spherical double row roller bearing consists of an outer ring with two raceways, a combined inner ring, double row rolling elements and a cage.
Features: The outer spherical double row roller bearing has two structures: sliding bearing and positioning bearing. The outer ring has self-aligning effect, the sliding bearing bears high radial load and allows axial sliding, and the positioning end can also bear bidirectional axial load while bearing particularly large radial load. It has a large carrying capacity.
Main application: Iron and steel industry → beneficiation ball mill; cement industry → ball mill, dry ball mill; mining industry → mining ball mill; ceramic industry→ceramic ball mill.
Spherical Roller Bearing for Ceramic Ball Mill
Bearing Model | ID mm | OD mm | W mm | Weight kg | Material |
53864CAF3/C3W33 | 320 | 620 | 200 | 295 | GCr15SiMn |
53868CAF3/C3W33 | 340 | 620 | 200 | 280 | GCr15SiMn |
53872CAF3/C3W33 | 360 | 620 | 224 | 350 | GCr15SiMn |
53876CAF3/C3W33 | 380 | 660 | 240 | 380 | GCr15SiMn |
53968CAF3/C3W33 | 340 | 640 | 200 | 310 | GCr15SiMn |
23268CA/C3W33 | 340 | 620 | 224 | 300 | GCr15SiMn |
23268CA/X3C3W33 | 340 | 650 | 200 | 350 | GCr15SiMn |
23272CA/C3W33 | 360 | 650 | 232 | 330 | GCr15SiMn |
23276CA/C3W33 | 380 | 680 | 240 | 380 | GCr15SiMn |
23176CA/C3W33 | 380 | 620 | 194 | 240 | GCr15SiMn |
23176CA/X3C3W33 | 339 | 620 | 194 | 280 | GCr15SiMn |
22260CA/X3C3W33 | 300 | 580 | 185 | 250 | GCr15SiMn |
23184CA/X3C3W33 | 420 | 680 | 255 | 360 | GCr15SiMn |
23172CA/X3C3W33 | 360 | 620 | 200 | 275 | GCr15SiMn |
23172CAF3/X3C3W33 | 360 | 620 | 200 | 275 | GCr15SiMn |
23288CA/X3C3W33 | 440 | 820 | 290 | 650 | GCr15SiMn |
23288CAF3/X3C3W33 | 440 | 820 | 290 | 650 | GCr15SiMn |
231/500CA/C3W33 | 500 | 830 | 264 | 567 | GCr15SiMn |
231/500CAF3/C3W33 | 500 | 830 | 264 | 567 | GCr15SiMn |
231/500CAF3/X2W33 | 500 | 830 | 290 | 610 | GCr15SiMn |
24192CA/C3W33 | 460 | 760 | 300 | 560 | GCr15SiMn |
24192CAF3/C3W33 | 460 | 760 | 300 | 560 | GCr15SiMn |
24084CA/C3W33 | 420 | 620 | 200 | 202 | GCr15SiMn |
24092CA/C3W33 | 460 | 680 | 218 | 280 | GCr15SiMn |
24096CA/C3W33 | 480 | 700 | 218 | 290 | GCr15SiMn |
24096CAF3/C3W33 | 480 | 700 | 218 | 290 | GCr15SiMn |
Spherical Roller Bearing for Mining & Cement Ball Mill
Bearing Model | ID mm | OD mm | W mm | Weight kg | Material |
230/500CAF3/X3C3W33 | 500 | 760 | 170 | 285 | GCr15SiMn |
230/500CAF3/C3W33 | 500 | 720 | 167 | 228 | GCr15SiMn |
230/530CAF3/C3W33 | 530 | 780 | 185 | 300 | GCr15SiMn |
230/560CAF3/C3W33 | 560 | 820 | 195 | 363 | GCr15SiMn |
230/600CAF3/C3W33 | 600 | 870 | 200 | 442 | GCr15SiMn |
230/630CAF3/C3W33 | 630 | 920 | 212 | 470 | GCr15SiMn |
239/690CAF3/C3W33 | 690 | 900 | 170 | 380 | GCr15SiMn |
239/695CAF3/C3W33 | 695 | 950 | 180 | 400 | GCr15SiMn |
239/695BCAF3/C3W33 | 695 | 950 | 200 | 420 | GCr15SiMn |
239/695B2CAF3/C3W33 | 695 | 950 | 230 | 490 | GCr15SiMn |
230/710CAF3/C3W33 | 710 | 1030 | 236 | 660 | GCr15SiMn |
239/710CAF3/C3W33 | 710 | 950 | 180 | 372 | GCr15SiMn |
239/700CAF3/C3W33 | 700 | 950 | 185 | 380 | GCr15SiMn |
230/750CAF3/W33 | 750 | 1090 | 250 | 789 | GCr15SiMn |
239/750CAF3/C3W33 | 750 | 1000 | 185 | 422 | GCr15SiMn |
230/800CAF3/C3W33 | 800 | 1150 | 258 | 870 | GCr15SiMn |
249/800CAF3/C3W33 | 800 | 1060 | 258 | 636 | GCr15SiMn |
239/800CAF3/C3W33 | 800 | 1060 | 195 | 490 | GCr15SiMn |
239/800CAF3X3/C3W33 | 800 | 1060 | 210 | 550 | GCr15SiMn |
239/800CAF3X2/C3W33 | 800 | 1100 | 250 | 520 | GCr15SiMn |
239/800CAF3X1/C3W33 | 800 | 1090 | 230 | 500 | GCr15SiMn |
230/850CAF3/C3W33 | 850 | 1220 | 272 | 1074 | GCr15SiMn |
239/850CAF3/C3W33 | 850 | 1120 | 200 | 560 | GCr15SiMn |
230/900CAF3/C3W33 | 900 | 1280 | 280 | 1175 | GCr15SiMn |
239/900CAF3X2/C3W33 | 900 | 1250 | 250 | 1150 | GCr15SiMn |
239/900CAF3/C3W33 | 900 | 1180 | 206 | 625 | GCr15SiMn |
239/950CAF3/C3W33 | 950 | 1250 | 224 | 772 | GCr15SiMn |
230/1000CAF3/C3W33 | 1000 | 1420 | 308 | 1580 | GCr15SiMn |
239/1000CAF3/C3W33 | 1000 | 1320 | 236 | 920 | GCr15SiMn |
239/1000CAF3B/C3W33 | 1000 | 1320 | 308 | 1000 | GCr15SiMn |
239/1000CAF3X2/C3W33 | 1000 | 1300 | 240 | 980 | GCr15SiMn |
249/1020CAX3/C3W33 | 1020 | 1320 | 300 | 1070 | GCr15SiMn |
230/1060CAF3/C3W33 | 1060 | 1500 | 325 | 1840 | GCr15SiMn |
230/1120CAF3/C3W33 | 1120 | 1580 | 345 | 2190 | GCr15SiMn |
230/1180CAF3/C3W33 | 1180 | 1660 | 355 | 2458 | GCr15SiMn |
240/1180CAF3/C3W33 | 1180 | 1660 | 475 | 1350 | GCr15SiMn |
239/1180CAF3/C3W33 | 1180 | 1540 | 272 | 1310 | GCr15SiMn |
249/1180CAF3/C3W33 | 1180 | 1540 | 355 | 1775 | GCr15SiMn |
230/1250CAF3/C3W33 | 1250 | 1750 | 375 | 2850 | GCr15SiMn |
239/1250CAF3/C3W33 | 1250 | 1630 | 280 | 1605 | GCr15SiMn |
239/1280CAF3/C3W33 | 1280 | 1590 | 300 | 1200 | GCr15SiMn |
206/1300CAF3/C3W33 | 1300 | 1560 | 150 | 554 | GCr15SiMn |
239/1400CAF3/C3W33 | 1400 | 1820 | 315 | 2170 | GCr15SiMn |
230/1440CAF3/C3W33 | 1440 | 1950 | 400 | 2550 | GCr15SiMn |
249/1500CAF3/C3W33 | 1500 | 1820 | 315 | 1700 | GCr15SiMn |
239/555CAF3/C3W33 | 555 | 745 | 120 | 238 | GCr15SiMn |
230/560CAF3X1/C3W33 | 560 | 800 | 185 | 357 | GCr15SiMn |
239/895CAF3/C3W33 | 895 | 1135 | 160 | 480 | GCr15SiMn |
239/895CAF3X1/C3W33 | 895 | 1135 | 200 | 600 | GCr15SiMn |
239/895CAF3X2/C3W33 | 895 | 1135 | 206 | 650 | GCr15SiMn |
239/895CAF3X3/C3W33 | 895 | 1135 | 260 | 738 | GCr15SiMn |
239/895CAF3X4/C3W33 | 895 | 1140 | 206 | 857 | GCr15SiMn |
249/1000CAF3X3/C3W33 | 1000 | 1300 | 300 | 1050 | GCr15SiMn |
239/1195CAF3/C3W33 | 1195 | 1500 | 300 | 1500 | GCr15SiMn |
239/1020CAF3/C3W33 | 1020 | 1320 | 240 | 950 | GCr15SiMn |
249/1020CAF3/C3W33 | 1020 | 1320 | 300 | 1220 | GCr15SiMn |
249/1400CAF3X3/C3W33 | 1400 | 1820 | 400 | 2850 | GCr15SiMn |
Comparison of the advantages of the two bearings
Spherical Double Row Roller Bearings |
Spherical Roller Bearing |
|
StructralDesign | 1.The barrel of the mill must have a certain inclination, and the outer ring with a radian is designed to adjust the inclination and misalignment of the mill.
2. Thermal expansion and contraction occur during mill production, and the inner ring is designed without ribs, which solves the problem of thermal expansion and contraction encountered in the production process of the mill due to high material temperature and regional temperature differences. 3.The mill is fixed: the discharge end is designed with double gears, which satisfies the positioning function of the mill barrel and makes the operation more stable. The feed end adopts a design without ribs, which meets the telescopic function of the mill cylinder, and the running resistance is smaller. 4. Mill bearing lubrication: The outer ring of the bearing is designed with 3 positioning holes, and each hole has an oiling thread. It is more convenient for users to lubricate the problem. |
1. The centering of the inclination of the mill is completed by the self-aligning of the arc-shaped raceway of the self-aligning roller bearing.
2.It does not have telescopic function, and is suitable for constant temperature environment and non-temperature materials. 3. The inner ring of the self-aligning roller bearing used at both the inlet and outlet ends of the mill has double gear sides, both of which have the positioning function. There is no axial sliding function. 4. The self-aligning roller has three oil holes |
Load Capacity | The mill is subject to high radial load: we use two rows of linear raceway design, with more contact surfaces to carry high load and reduce impact load, so as to achieve the bearing weight and impact load required by the mill. | The spherical roller bearing raceway is an arc-shaped contact surface with a small contact area. Large mills have limited weight load capacity. |
Life Span | The service life can generally reach 10-12 years. | The general service life of spherical roller bearings is 3-5 years |
Energy saving | The double raceway design has smaller running resistance and significantly lower starting resistance, which can save electric energy; it is convenient for maintenance and saves a lot of water resources. | The energy-saving effect of the curved raceway contact surface is not obvious |
Spherical Double Row Roller Bearings
Ball mill |
Bearing number | ID mm | OD mm | W mm | Weight kg |
1.5M Feed |
NNU560Y | 560 | 830 | 180 | 335 |
Discharge |
NNUP560Y | 560 | 830 | 200 | 340 |
1.83M Feed | NNU695Y | 695 | 1000 | 230 | 573 |
Discharge |
NNUP695Y | 695 | 1000 | 255 | 590 |
2.2M Feed | NNU895Y | 895 | 1200 | 240 | 781 |
Discharge |
NNUP895Y | 895 | 1200 | 265 | 787 |
2.4M Feed | NNU1000Y | 1000 | 1300 | 280 | 997 |
Discharge |
NNUP1000Y | 1000 | 1300 | 300 | 1010 |
2.6M Feed | NNU1200Y | 1200 | 1600 | 280 | 1350 |
Discharge |
NNUP1200Y | 1200 | 1600 | 330 | 1420 |
3.2M Feed |
NNU1400HY | 1400 | 1800 | 280 | 2300 |
Discharge |
NNUP1400HY | 1400 | 1800 | 310 | 2400 |
Case Show
Background: Ball mills are widely used in the mineral processing and grinding industry. Their operation is realized by the friction and sliding of the hollow shaft and the bearing pad. However, the bearing pad is used in conditions with a lot of dust, high friction coefficient and high temperature, and bears the impact of the cylinder load, so the bearing pad is prone to damage. Phenomena such as "burning tiles" affect the normal operation of the ball mill.
Customer keywords: high temperature, heavy load, burning tiles, high dust, frequent shutdowns, high maintenance costs.
01. Bearing selection: NNU895Y3 at the feed end, NNUP895Y3 at the discharge end
According to the customer's working conditions, the ball mill is composed of a cylinder, a hollow shaft, a main bearing seat, and a bearing bush. An axial force will be generated when bearing a load, and a bearing with a large bearing capacity needs to be selected. We have designed the outer spherical double row roller bearing with strong load capacity, good impact resistance, convenient lubrication, high reliability, fixed to the grinding machine, and can still work normally when moving axially. Through life calculation, there is no problem in verifying 43800 hours.
02. Design optimization:
According to the customer's working conditions:
1. The original ball mill uses the hollow shaft and the bearing bush for sliding friction transmission, and the thin grease forms an oil film for circulation lubrication. In actual use, as the material increases, the bearing bush load increases. If the heat generated by friction is not dissipated in time, it will produce "Burning tile" accident, so we improved the sliding friction of the bearing pad, adopted the rolling friction design, and designed a double row roller bearing.
2. The dry ball mill will elongate due to the high temperature of the incoming material and the temperature generated by the operation. Cause the cylinder body to move in two directions and run unstable. Therefore, the movement and fixation of the mill cylinder are designed, the inlet is designed without ribs, and the outlet is designed with double ribs, which satisfy the stable operation of the cylinder.
3. Due to its own weight and the impact of grinding steel balls and steel forgings, the cylinder is bent and deformed to produce deflection, which requires the rolling bearing to be self-aligning, otherwise the cylinder is not in the same axis, resulting in damage to the bearing. Therefore, we have designed the self-aligning requirements of the rolling bearing. The outer diameter of the outer ring of the bearing is designed in an arc shape, which solves the problem of the cylinder being out of alignment.
03. Result demonstration:
By combining the application conditions of the equipment, we have designed a new type of ball mill bearing to meet the customer's needs. The downtime caused by the customer's "burning of tiles" fault is greatly reduced, saving users 80% -90% of lubricating oil, over 8% of electricity, and a comprehensive energy saving of over 10% -15%. The power of the electric motor used in the ball mill can be reduced by 13% -20%, and the loading capacity of the grinding body can be increased by 15% -20%, improving the operation rate of the ball mill.